What is 3M Safety & Industrial Manager?
In 2016, the Safety & Inspection Manager (SIM) product was launched to help environmental health and safety (EHS) managers connect with data about their equipment, their workers, and compliance activities they perform every day.
SIM aims to reduce administrative burdens and decrease time spent spent inspecting and managing assets.
Organizations Using SIM
Assets Managed
164
131,000+
Workers Added
Inspections Created
4,250+
700,000+
Inheriting Legacy
SIM was built quickly to address an immediate market need, but for a tool that promised increased productivity, it was confusing, difficult to use, and inconsistent.
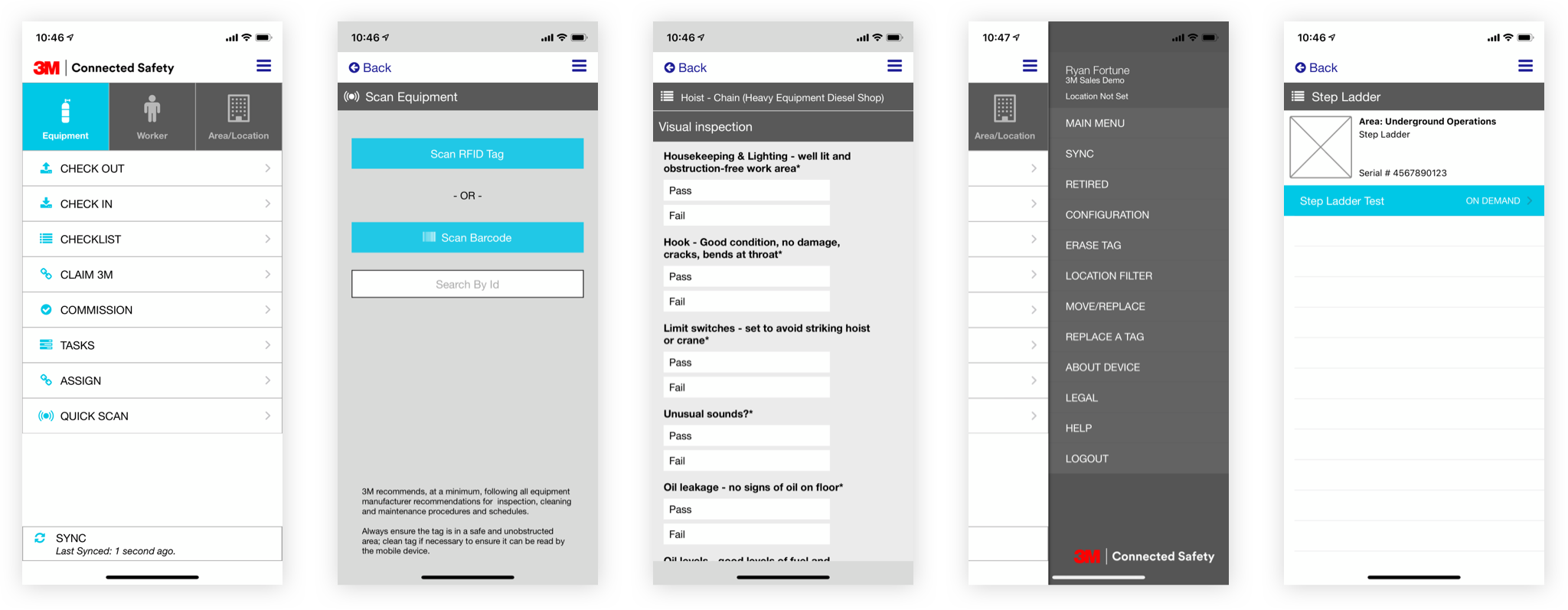
A customer baseline study was conducted by design research in Spring 2019 (prior to my arrival at 3M). The team gathered results from 89 customers and the results were clear: usability was the core pain point.
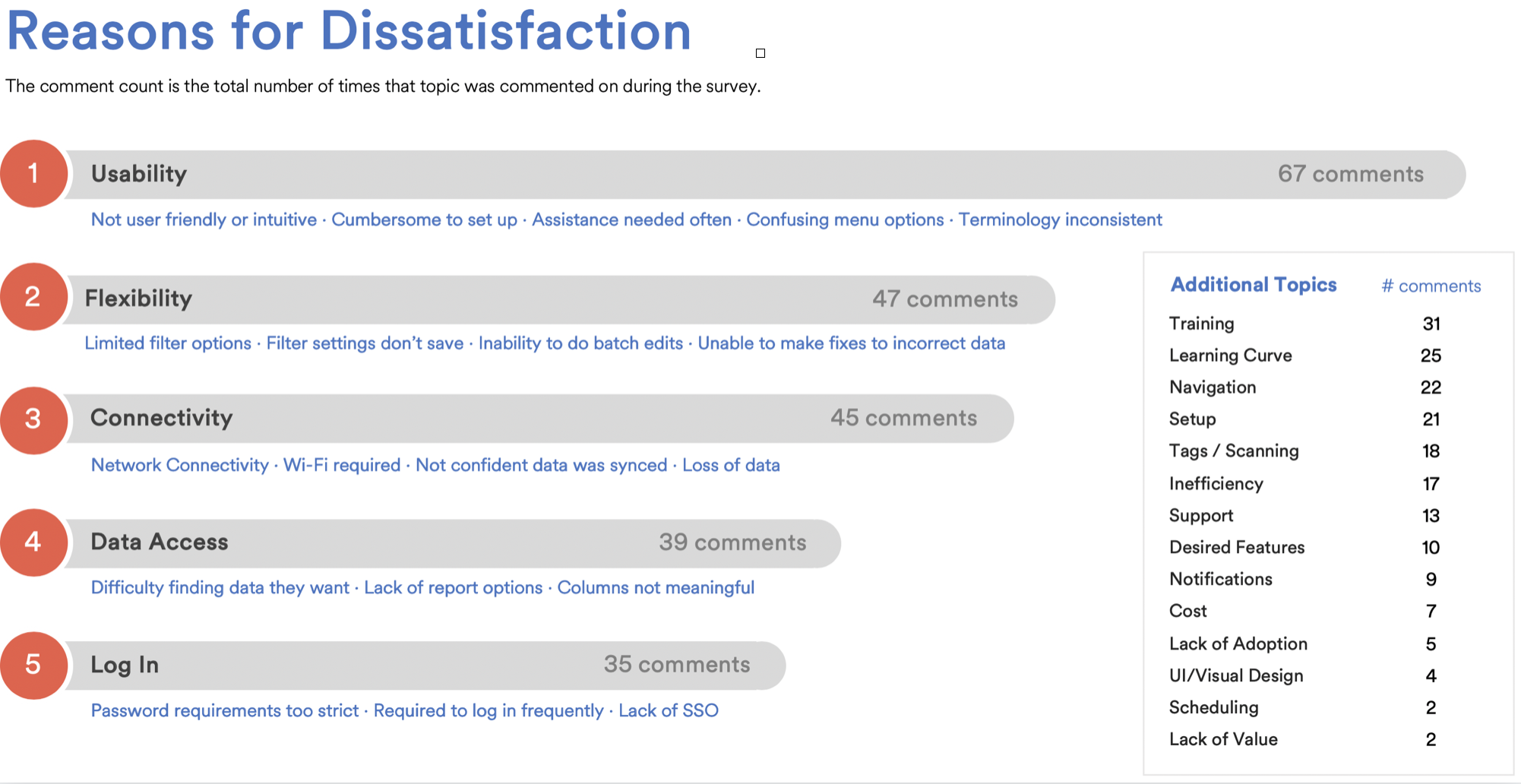
Additional findings included:
NPS Score
-22 out of 100
(high 40s is software industry standard, 76% of participants were passive or detractors)
SUS Score
64.2
(>68 is below average)
Uncovering misalignment amongst product leadership
Our internal stakeholders were not aligned around the core value SIM, as a product, provides to our customers. They described the target customer as...
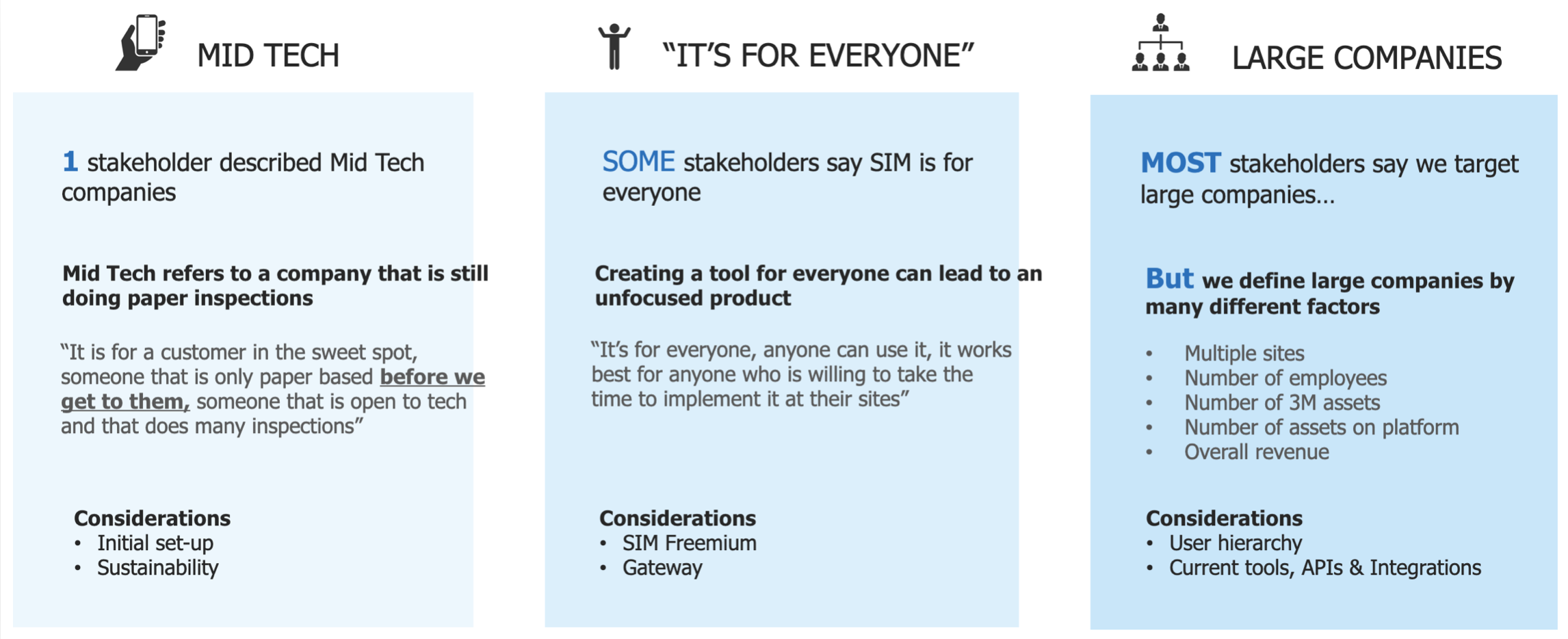
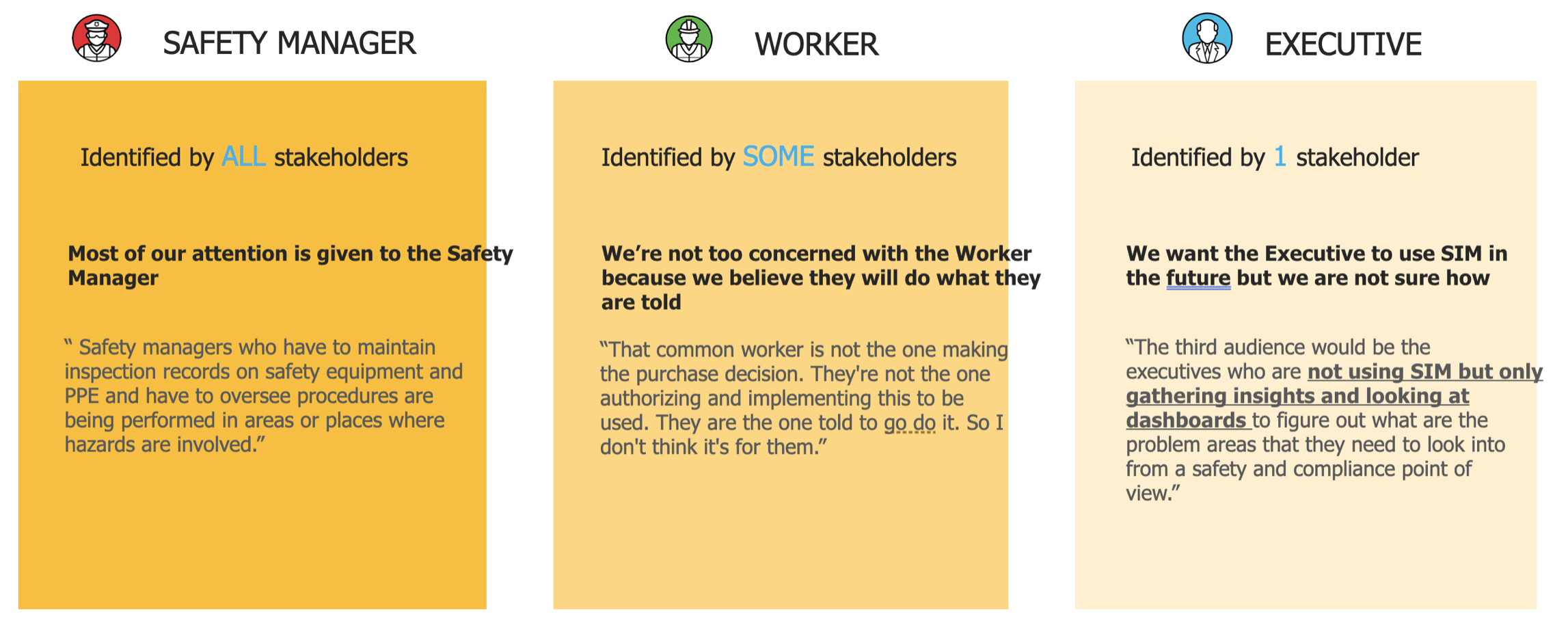
The core product owner helped synthesize a more focused view of the customer...
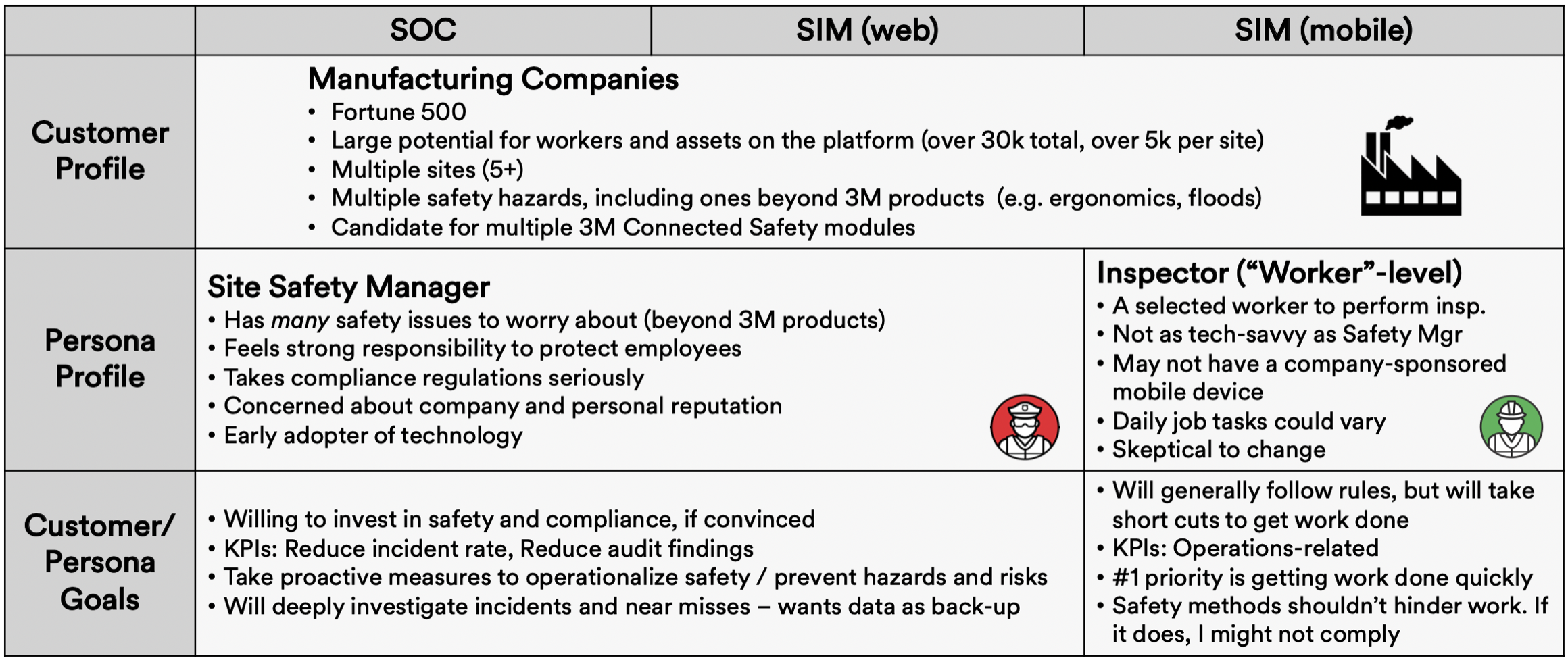
By this time, we had gathered enough buy-in to kick off a redesign effort for both the web and mobile experiences. I will be sharing the mobile redesign story here, but I also redesigned the web experience with an emphasis on simplifying the inspection creation experience.
Narrowing Focus
The timing of the redesign coincided with an already-in-progress product initiative to create one cohesive Connected Safety platform (of which SIM was a standalone product).
We began the formative discovery process to chart an intentional path and focus for a redesign.
Our redesign journey started with:
- Internal empathy workshop
- On-site observations with customers
Elevating empathy
As mentioned above, one of the reasons SIM was failing customers was due to disconnect between product leaders. We soon learned most had never seen or used the software.
I facilitated a simulated customer onboarding experience with our core product team and a few key stakeholders. The stakeholders role-played as customers. Our account engineer (onboarding specialist) guided our stakeholders through the implementation process while product owners, researchers, and designers noted positive, neutral, and negative observations.
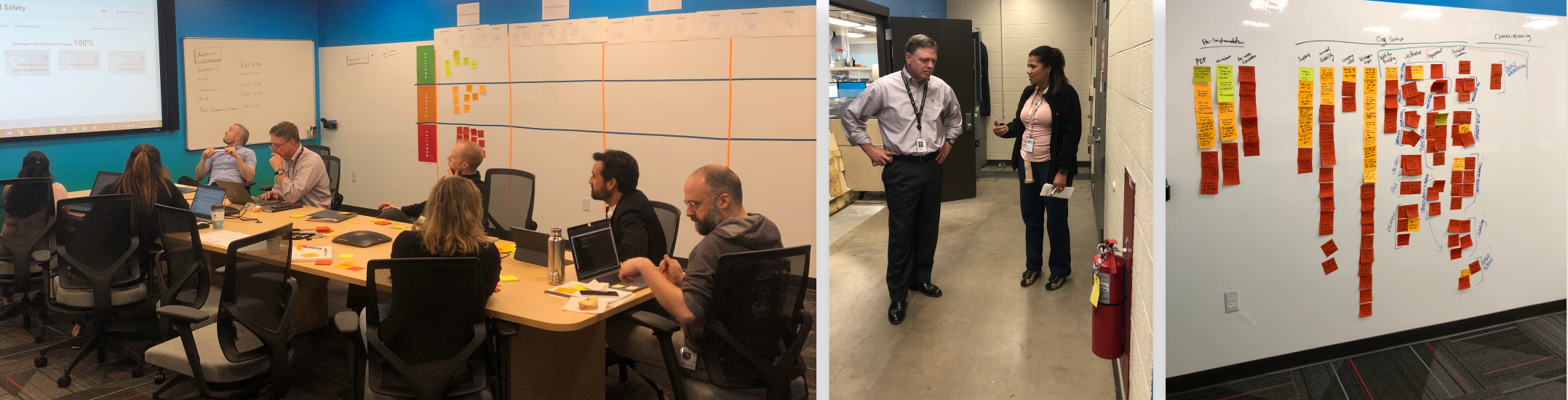
Visiting our customers
Next, we observed safety managers and inspectors using SIM while they performed daily tasks. They each had their own unique way of setting up their work sites to accommodate inspections – some were more effective than others. One thing, however, remained – they all wanted to get their work done quickly and efficiently, and felt SIM was inhibiting their ability to accomplish that.
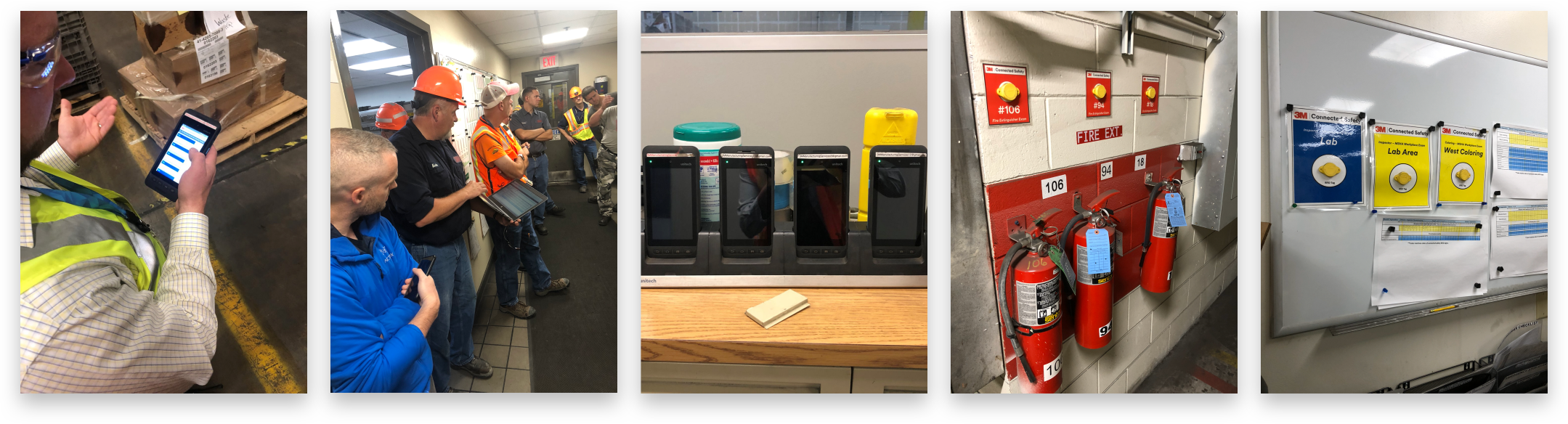
Unveiling the findings
In collaboration with design research, I created a list of recommendations for improving the SIM experience based on observed (and stated) problems.
Recommendations:
- Provide customers the flexibility to set up SIM in the order they see fit – there is not a one-size-fits-all method
- Minimize the required up front work – the faster users can begin performing inspections and scanning equipment, the better
- Provide multiple pathways to organize assets – the rigidity of the SIM system does not match real world needs
- Provide wayfinding capabilities – inspectors typically follow a route when inspecting assets, let's give them the most efficient path to do so
- Allow inspectors to see what inspections have been performed and what still needs to be inspected
These recommendations were later scoped by the business owners to align with the planned integration work and to accommodate engineering resourcing constraints.
Scoped recommendations:
- Streamline and simplify the commissioning process
- Provide multiple ways to organize assets
- Allow inspectors to see what inspections have been performed and what still needs to be inspected
Defining the Vision
In parallel with business owners, we aligned on the initial vision for the redesign.
Primary goals...
- Update the mobile UI to match the Connected Safety platform design system to provide a cohesive experience
- Streamline commissioning to allow for greater number of assets to be added to the Connected Safety platform
- Strengthen the core foundation of the app to pave the way for future enhancements
This redesign is not...
- Addressing all known usability issues
Design principles...
- Humanize the Experience – use human language, match the safety inspector mental model
- Celebrate Progress – make potentially painful processes feel like an accomplishment, incentivize for deeper product usage
- Fundamentals First – obsess over the basics, deeply understand and craft solid foundational experiences, proudly build for today... and for the future
Exploration
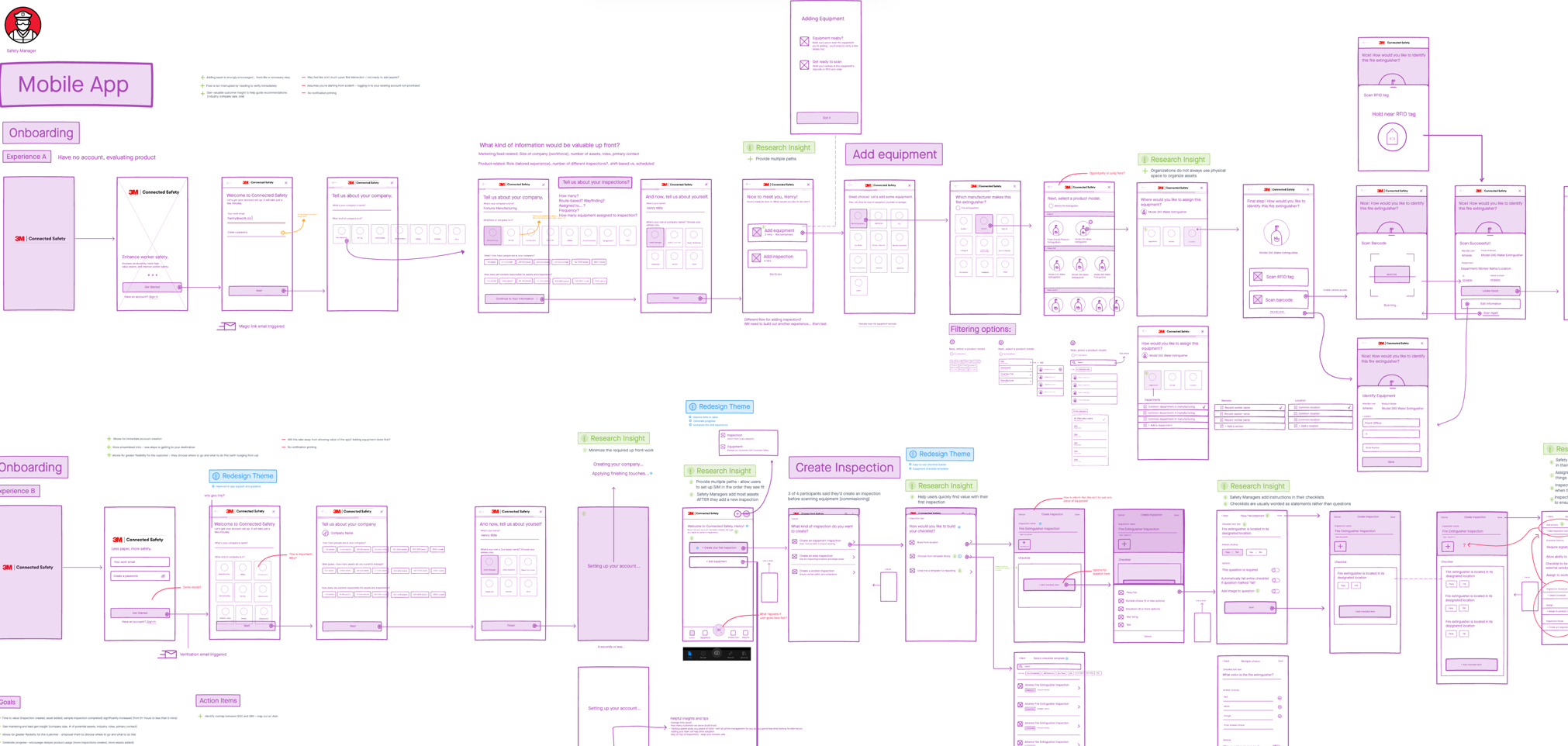
Streamlining commissioning
The true focus for the first iteration was to decrease the time spent adding new equipment to a worksite.
Frequently, users would begin the commissioning process only to hit a roadblock: missing or incorrect product models. Product models were only eligible to be created in the web experience.
I designed an experience that allowed product model creation on mobile to avoid any gaps in the commissioning flow and allow managers to add as many assets as desired without interruption.
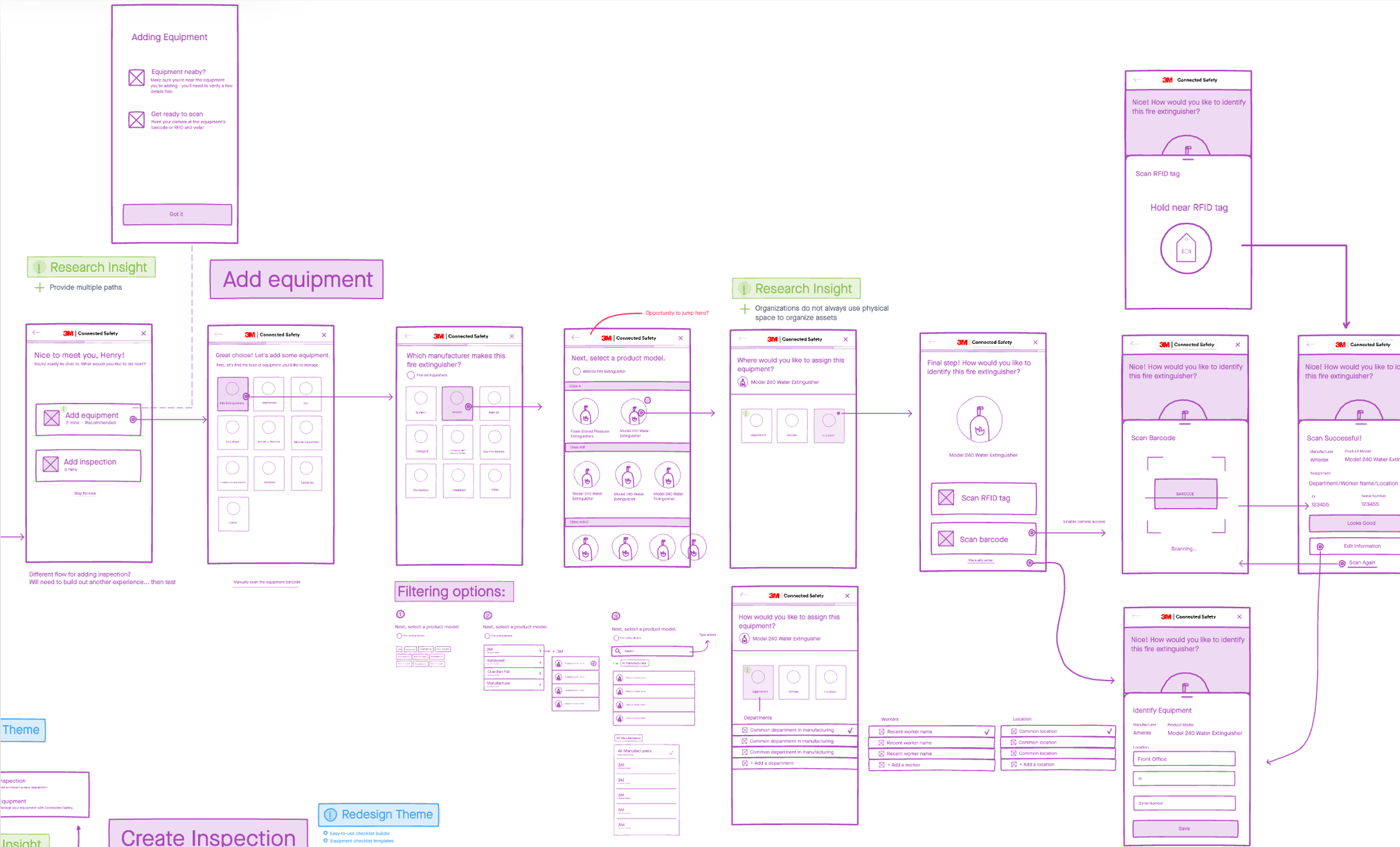
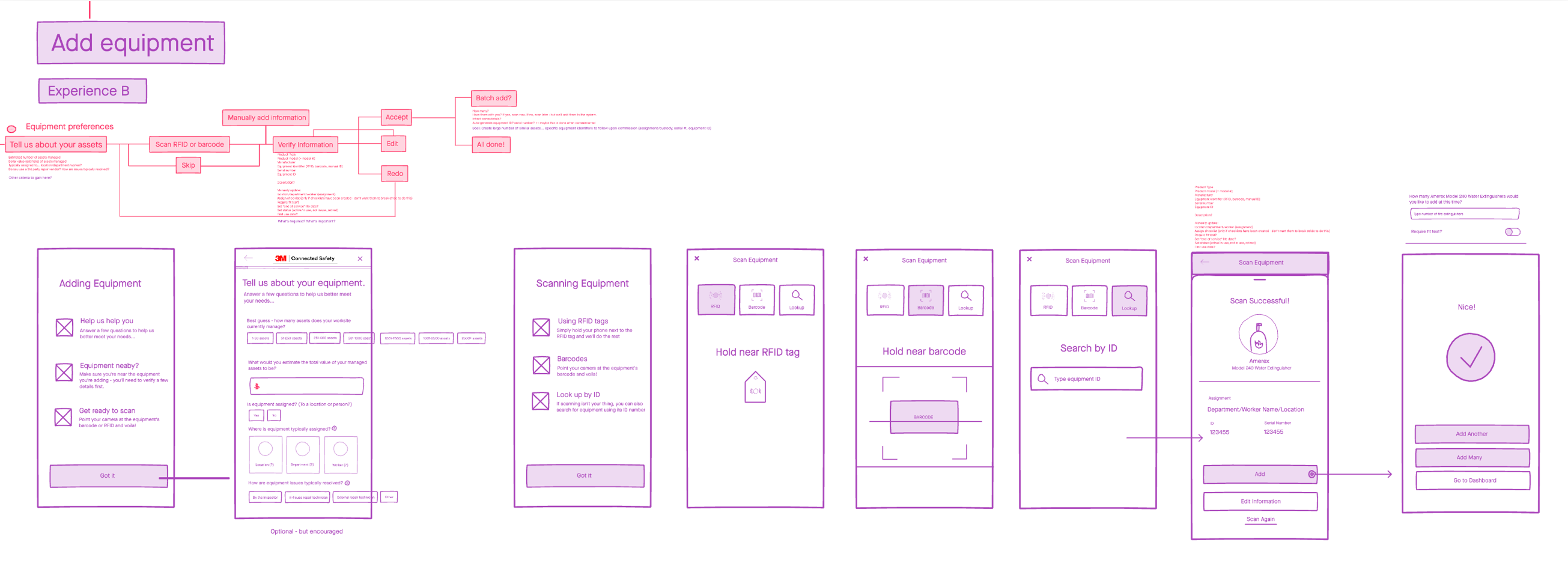
Prototyping
After a handful of working sessions with the core product team, both workflows were deemed viable options and marked improvements over the current experience. We wanted to get a better feel for how the proposed commissioning flows felt to use, so I built a prototype with Sketch and InVision.
This video shows workflows for adding three separate, but similar, fall harnesses:
Three key commissioning priorities
1. Avoid duplication
Product names are very similar often with only a few variations such as size, weight, or model number.
I designed an experience with intentional friction requiring a user to exhaust all methods of searching for existing models before they could add a new model.
2. Re-use known details
Safety managers receive shipments of personal protective equipment (PPE) in bulk and want to add many assets at one time. SIM only supported adding assets one-by-one. This was a constraint I needed to work within for phase 1.
Once the first piece of equipment had been added, we were able to pre-populate details that were frequently similar such as product model name, category, and assigned inspection. This meant the only detail that may differ from one piece of equipment to the next might be the area to which it is assigned. Re-using details could significantly decrease the amount of time taken to commission.
3. Harness the power of RFID tags
3M products, specifically fall harnesses, typically have RFID tags. The tags arrive from the manufacturer with pre-written equipment details needed for commissioning. Instead of requiring users to manually enter these details, we were able to harness (pun 😏) the power of RFID tags by pulling in all the pre-written data after the first scan with mobile app.
What did customers think?
I conducted eight usability studies. The results were very encouraging and the team decided to move forward with this experience for phase 1.
Customers who added new equipment successfully
8 of 8
Customers who added new product models without intervention
6 of 8
Average time to add three pieces of equipment plus new model
>3 mins
Final UI
The commissioning experience was only one piece of the re-design. As this project also consisted of a complete re-design, there are hundreds of different screens, use cases, and interactions designed in parallel to the commissioning flow. I prioritized usability and workflow improvements.
This is a collection of final designs (copy pending).
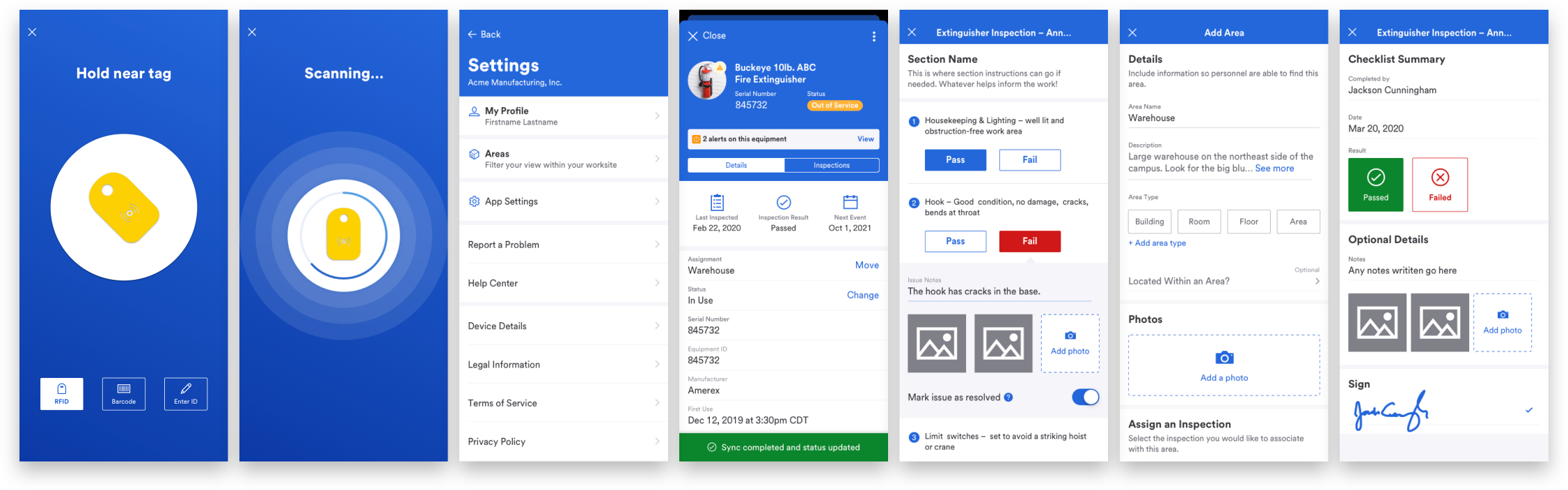
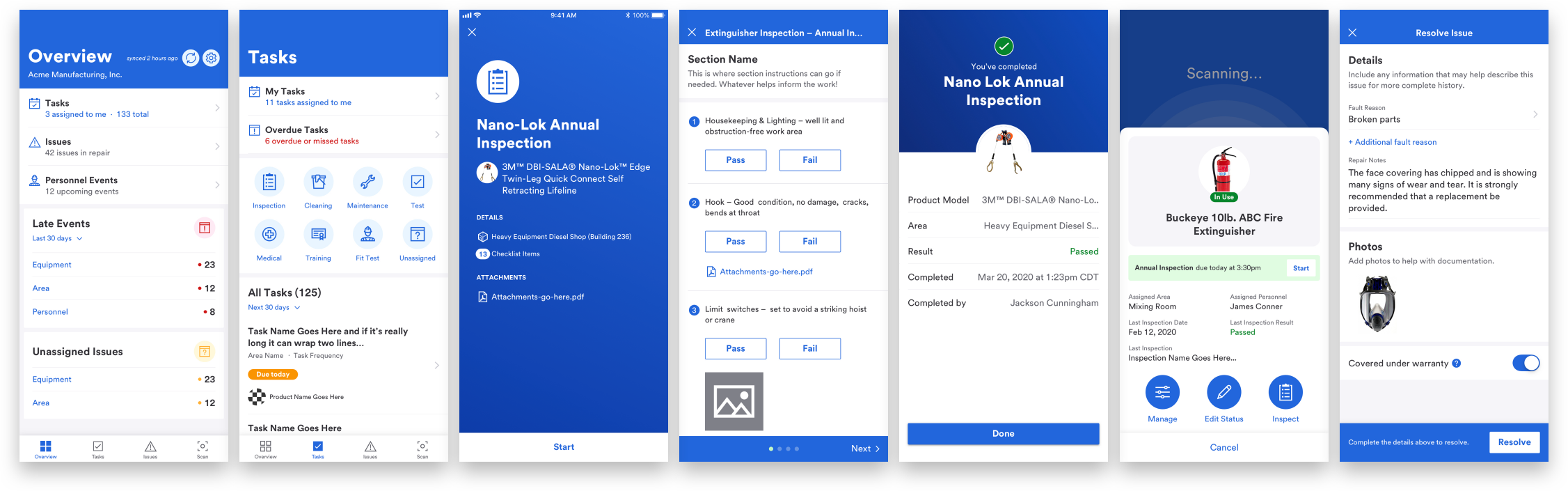
Outcome
Formerly: This project is currently in development with a planned launch in October 2021.
Update: This project was sunset by 3M after an internal restructure in late 2021.
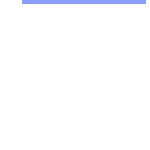